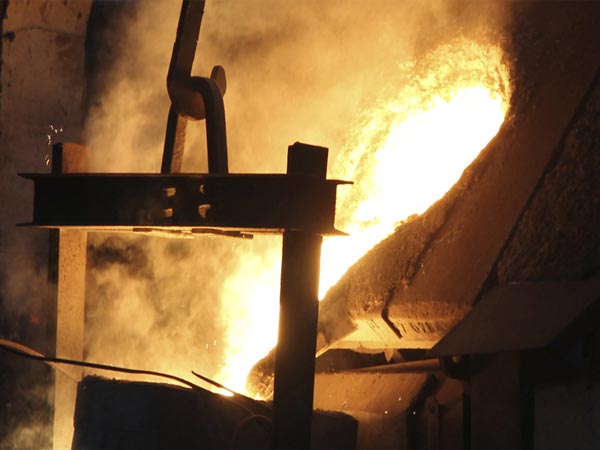
The high-alloy white irons are primarily used for abrasion resistant applications and are readily cast in the shapes needed in machinery used for crushing, grinding and general handling of abrasive materials. The large volume of eutectic carbides in their microstructures provides the high hardness needed for crushing and grinding other materials. The metallic matrix supporting the carbide phase in these irons can be adjusted by alloy content and heat treatment to develop the proper balance between resistance to abrasion and the toughness needed to withstand repeated impact.
All high-alloy white irons contain chromium to prevent formation of graphite on solidification and to ensure the stability of the carbide phase. Most also contain nickel, molybdenum, copper or combinations of these alloying elements to prevent the formation of pearlite in the microstructure. While low-alloyed pearlite white iron castings develop hardness in the range 350 to 550 HB, the high-alloyed white irons range from 450 to 800 HB.
High, Cr cast irons are alloys based on the Fe-Cr-C system, usually in the range from 10 to 30% Cr and from 1.8 to 4% C. Commercial alloys contain up to 1% residual Si and additions of Mn, Mo, Ni and Cu to increase hardenability. In this range of compositions most of the alloys solidify as mixtures of austenite and M7C3 carbides. Though high amounts of carbides and high matrix hardness tend to promote wear resistance, these parameters must be balanced according to the applications, because of the brittle behaviour of the carbides.
The high-chromium irons designated for use at elevated temperatures fall into one of three categories, depending upon the matrix structure:
- The martensitic irons alloyed with 12 to 28% Cr
- The ferritic irons alloyed with 30 to 34% Cr
- The austenitic irons which in addition to containing 15 to 30% Cr also contain 10 to 15% Ni to Stabilize the austenitic phase