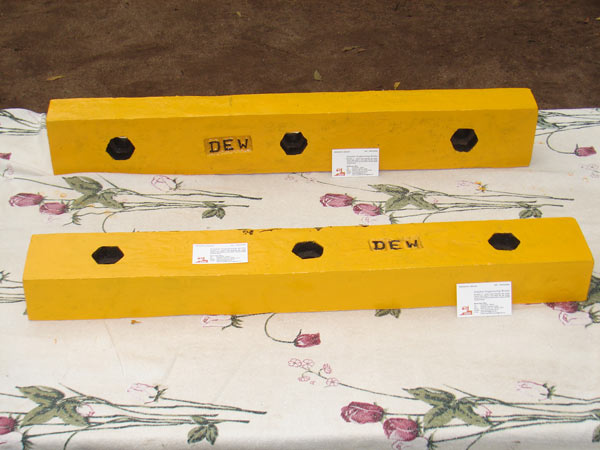
The first austenitic manganese steel was developed in 1882 by Robert Abbott Hadfield. Hadfield had done a series of test with adding ferro-manganese containing 80% manganese and 7% carbon to decarbonised iron. Increasing manganese and carbon contents led to increasing brittleness up to 7.5% manganese. At manganese contents above 10% however, the steel became remarkably tough. The toughness increased by heating the steel to 1000 deg C followed by water quenching, a treatment that would render carbon steel very brittle. The alloy introduced commercially contained 1.2% carbon (C) and 12% manganese (Mn) in a ratio of 1:10. This composition is used even today, and the austenitic manganese steel is still known as Hadfield steel. The steel was unique since it exhibited high toughness, high ductility, high work hardening ability and excellent wear resistance. Because of these properties Hadfield’s austenitic manganese steel (AMS) gained rapid acceptance as a useful engineering material.
Austenitic manganese steels have a proven high resistance to abrasive wear including blows and metal-to-metal wear, even though they have a low initial hardness. These steels are supposed to work harden under use and thus give a hard wear resistant surface, but it has been reported that these steels have a good wear resistance in components even without heavy mechanical deformation.
Hadfield’s austenitic manganese steel is still used extensively, with minor modifications in composition and heat treatment, primarily in the fields of earthmoving, mining, quarrying, oil well drilling, steelmaking, railroading, dredging, lumbering and in the manufacture of cement and clay products. Austenitic manganese steel is used in equipment for handling and processing earthen materials (such as rock crushers, grinding mills, gredge buckets, power shovel buckets and teeth, and pumps for handling gravel and rocks). Other applications include fragmentizer hammers and grates for automobile recycling and military applications such as tank track pads etc.
PRODUCT SPECIFICATION
- Solution treated casting
- Water quenched at 1050 C
- Agitation facility created for maintaining water temperature at 80 C while quenching
- Bend-tested specimen test bar provided on customer's insistence
- Hardness assurance
Uses :
In Crusher hammers, liner plates, tooth points etc.Uses :
Specifically used for machinery with high working temperature application like shell liner of cement industries, hammers in crushing equipment etc.Uses :
For continuous heavy duty crushing parts like grate plate liners.Uses :
In wear & abrasion resistant parts of earth moving equipment e.g. tooth points in pay loaders, excavators etc.- Casting Weight:
- Maximum weight = 200 Kgs. (Soon expanding to 350 Kgs.)
- Production capacity:
- 75 tons per month (Soon expanding to 150 tons per month)
- Captive power:
- 150% of Electric Board Supply
- Finishing Processes:
- Gas cutting
- DC Arc Cutting
- Gringing and Fettling
- Heat Treatment [1050 C] with temperature control and recorder.
- Water Quenching with cooling tower and agitator (temp. control at 50 C max.)
- Oil Quenching
- Sand Blasting
- Shot Blasting
- Quality Control
- Fully equipped Wet lab
- Sand Lab
- Microscope with polishing equipment
- Spectro Analyzer
- UTM, BHT, PHT (UTM: Universal Testing Machine, BHT: Brinell Hardness Tester, PHT: Poldi Hardness Tester)
- Photometric Analysis
- Radiographic Testing (by certified external agencies)